Concrete Flooring
.jpg)
Polished Concrete Flooring
Polished concrete undergoes mechanical grinding and polishing to achieve the desired sheen level. A densifier/hardener chemical is applied during polishing, penetrating the concrete and resulting in a harder, glossier, and dust-proof surface.
.jpg)
Properties & Uses
.png)
Polished concrete is predominantly utilized in schools, commercial buildings, and luxury homes because of its exceptionally high durability against wear and traffic. Due to the chemical hardening/densifying that accompanies the polishing process, this material requires low maintenance and upkeep, and it is very difficult to scratch or scuff.
Schools & Universities
Commercial Buildings
Luxury Homes
Types of Polished Concrete Flooring
.png)
CLASS A - Cement Fines/Cream
- Minimum Possible Cut Depth
- 85-95% Cement Fines with 5-15% Fine Aggregate
- Does not remove blemishes or imperfections
CLASS B - Fine Aggregate/Salt & Pepper
- +/- 1/16” Cut Depth
- 85-95% Fine Aggregate with 5-15% Blend of Cement Fines & Coarse Aggregate
- Lessens the appearance of surface blemishes
- Sand fines visible with little aggregate exposure
CLASS C - Coarse Aggregate/Deep Grind
- +/- 1/8” Cut Depth
- 80-90% Coarse Aggregate with 10-20% Blend of Cement Fines & Fine Aggregate
- Larger aggregates exposed
- Significantly reduces the visibility of imperfections
Installation Process
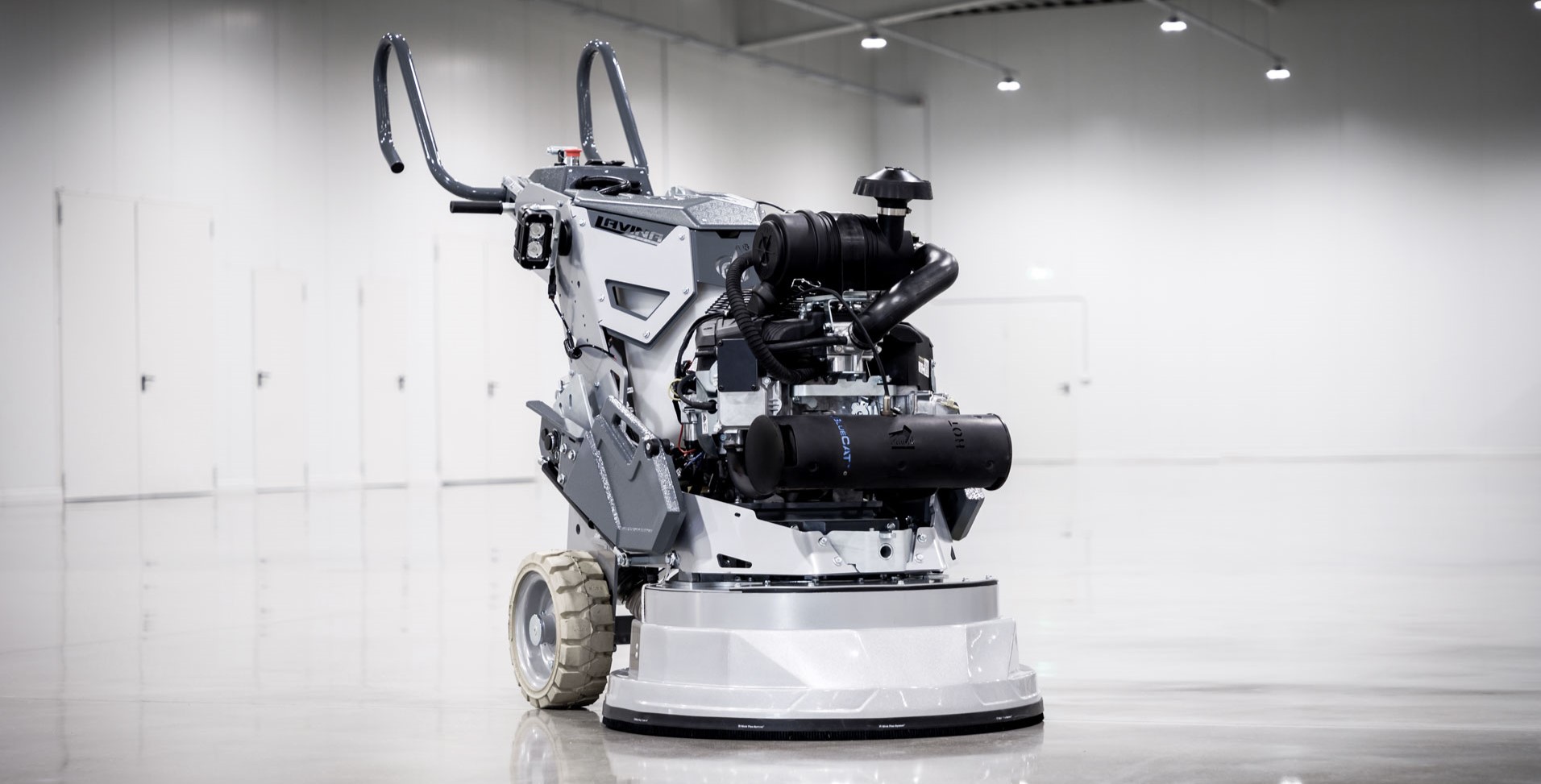
Typically installed prior to framing. Industrial grinding process utilizing diamond abrasives to abrade the concrete surface resulting in a smooth floor with options from semi gloss to high gloss. Because polished concrete is installed early in construction it is best practice to protect the concrete from spills and trade damage using www.goldiloxusa.com or similar.
Options
.jpg)
Dyes & Stains
These products penetrate the concrete to add vibrant colors and unique effects, enhancing the aesthetic appeal while maintaining the floor's natural texture.
Sealers
Sealers provide a protective layer that defends against moisture, stains, and wear, extending the lifespan and preserving the look of the concrete surface.
Guards
Shield offers an advanced, durable coating that guards against heavy traffic, chemical spills etc., ensuring the floor remains pristine under tough conditions.
%20(Medium).jpg)
Burnished
Burnished concrete flooring is a sleek and modern option renowned for its durability, resilience, and affordability. Through mechanical polishing, the surface achieves a smooth, glossy finish, enhancing its ability to withstand stains, scratches, and wear. Ideal for commercial spaces with high traffic, burnished concrete offers a practical and cost-effective flooring solution.
Properties & Uses
.jpg)
Burnished concrete is chemically hardened and burnished with high-speed rotary equipment, skipping the grinding and polishing steps of polished concrete. This results in a durable, shiny surface that's more affordable and still attractive.
Restaurants & Retail
Barndominiums
Contemporary Homes
Warehouse/ Facility/
Manufacturing Space
Types of Burnished Flooring
.png)
Chemically hardened and burnished
Chemically densified and hardened only without burnishing
Installation Process
.jpg)
Concrete surface is chemically hardened and densified using a liquid silicate often in the form of a Sodium or Lithium Silicate. This process increases the density and scratch resistance of the concrete surface while also reducing concrete "dusting" (natural breakdown of crystalline bond that holds cement particles together). Hardener is spray applied. Once cured, high speed burnishing will help to increase the sheen.
Options
.jpg)
Burnished
Non burnished and densified/ hardened only
Topical Guard or sealer
Stain & Seal
Stain and seal concrete flooring offers a unique blend of beauty and durability. Expert staining processes enhance the natural character of concrete, creating rich, translucent tones that mimic the look of stone or marble. Sealed for protection, the flooring is resistant to stains, spills, and wear, making it an ideal choice for both residential and commercial spaces seeking a stylish yet practical flooring solution.
%20(1).jpg)
Properties & Uses
.png)
Stained and sealed concrete combines penetrating stains and topical sealants to add color, sheen, and protection. Acid stains create organic color variations, and finish options include gloss, semi-gloss, and matte. These floors offer better spill protection than polished or burnished concrete but are more prone to scratching and require more maintenance.
Residential
Restaurant/Bar
Low to medium traffic commercial/retail setting
Types of Stained and Sealed Concrete
.png)
Interior stained concrete flooring
Exterior stained concrete
Sealed concrete (no stain or dye)
Installation Process
.png)
Most commonly installed later in construction to avoid excess scratching. Interior stained and sealed concrete should be installed after sheetrock. Exterior stained concrete should be installed at the very end of construction. Stain colorants are spray applied, allowed to dry, and then topped with a spray or roll applied sealer which should be allowed to cure a min of 72hrs prior to traffic.
Options
%20(Medium).png)
Chemical Acid Stain
Chemical reaction with the concrete surface. Chemical reaction produces natural mottling as each sq foot of concrete reacts slightly different from the next. Chemical staining actually chemically alters the color tone of the cement itself resulting in durable/UV stable coloring.
Water Based Stain
A more broad selection of color. Colorant it's absorbed into the pores of the concrete and are less durable and long lasting vs Chemical stains. Best used on exterior concrete that is more porous than interior hard troweled concrete.
Dyes
A very wide selection of colors. Very often dyes offer a more monolithic color tone vs chemical stains. Suitable for interior only.
Non-Skid Additives
.jpg)
Coating
Coating concrete flooring with materials like epoxy, polyurethane, or acrylic significantly enhances its durability, providing resistance to wear, chemicals, and moisture. Ideal for high-traffic and industrial areas, these coatings are easy to maintain and customizable.
Properties & Uses
.png)
Also referred to as resinous flooring, coatings are typically epoxy or urethane based, thick bodied membranes that coat the concrete surface. These coatings are 100% opaque and completely cover/mask the concrete beneath. Coatings range from decorative to industrial and can serve a wide range of uses. Coatings are not nearly as durable against vehicle traffic or abrasion compared to polished concrete and are typically reserved for use when protection from oils or other damaging liquids is the top priority over abrasion and traffic.
Types of Coated Concrete
.png)
Epoxy flake coat
Metallic epoxy
Pigmented epoxy
Polyaspartic
Urethane
Urethane Cement (harsh chemical)
Installation Process
.jpg)
- Roughen the concrete surface
- Check for moisture concerns
- Spray or roll apply the coating and let cure
- Coatings should be installed later in the construction process to avoid damage from trades
Options
.jpg)
Non-Skid Additives
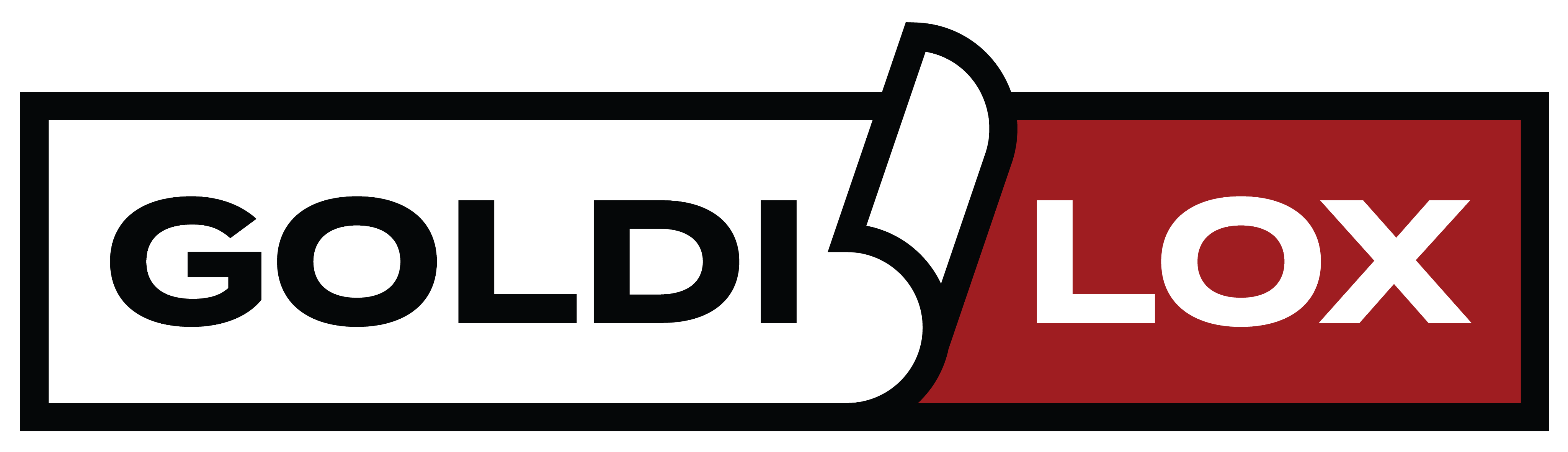
Protect your Concrete with Goldilox!
Goldilox is a durable, seamless, high traction floor covering that is temporarily glued in place to protect the concrete slab or concrete flooring beneath, and is simply peeled off at the end of construction.
.png)
Request a Quote
Experience the beauty and durability of our polished concrete floors and our other quality services. Contact us today for a free quote.
.jpg)